Improving Hydropower Operations with Digital Solutions
Using advanced tech solutions to manage critical operational tasks enables hydropower plant operators to prepare for future challenges while simultaneously building a profitable and sustainable business for the decades to come.
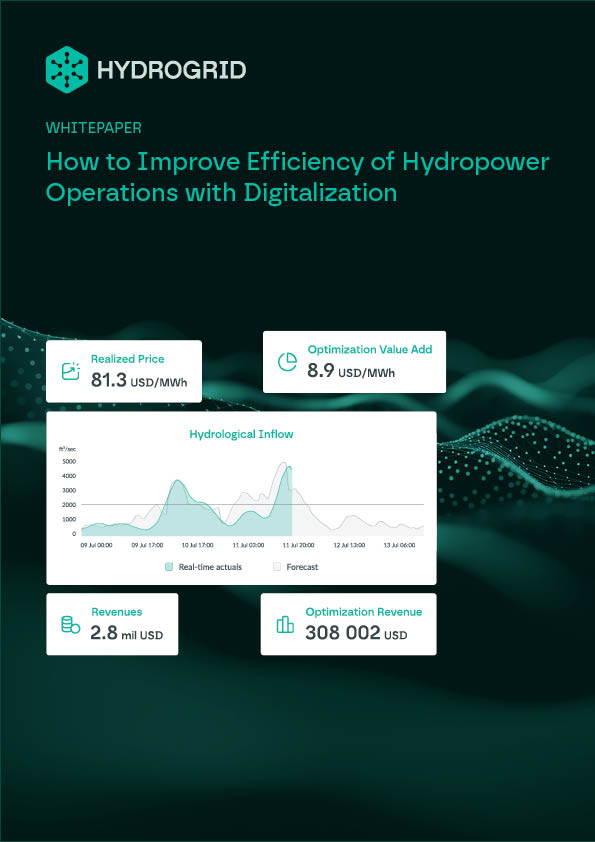
Improving efficiency is a clear and straightforward methodology that can bring numerous benefits to any business, regardless of the industry they are in. Even if a company holds a stable market position and is not particularly concerned about business performance, implementing operational improvements can deliver many benefits, primarily to its most important resource – people.
In the hydropower sector there is a range of factors which are driving change, forcing operators to seek ways to improve efficiency in key areas: from daily operational challenges, through revenue goals, to following regulatory constraints. On top of that, operators are left to the mercy of nature and its whims, which have been way more powerful in recent years, with long-lasting effects on the environment, but also on the infrastructure of the power plants.
Given the complexity of all these influencing factors and how interconnected they are, hydropower plant operators are often faced with a challenge of balancing multiple, constantly changing variables to create the right setup and balance, leading to improved business results, but also less headaches for everyone.
Fortunately, this is where technology comes to the rescue. Insisting on using proven, 50-year-old playbooks and procedures might seem like a safe bet for managing a hydropower plant, but faced with increased pressure from both internal and external stakeholders, many operators now turn to modern tech solutions to help them achieve operational excellence.
In this whitepaper we will try to answer the key question: how can hydropower plant operators reach new levels of efficiency and achieve more flexibility with existing resources through relying more on technology and the benefits it brings.
Navigating Operational Management Challenges
When you ask any hydropower plant manager what are the main causes of their headaches, quite a few things would come up, but the undisputed favorites are daily operation and maintenance (O&M) challenges. Juggling between the complex and intertwined realities of the hydrological uncertainties, equipment capacity and readiness, and the dynamic electricity market, operations managers often choose to stick to proven strategies and techniques.
Although it may seem it’s better to remain on the safe side and use proven models and plans, this approach leaves little or no space for noticeable improvements in operational efficiency or revenue increases. The term “we have always done it this way” has come to haunt many industries (for example, look at German car manufacturers and their decline in the past few years), so it’s just a matter of time when this ghost of doom will come to wreak havoc in hydropower.
To meet the demands of the market and the owners, many hydropower operators do production planning on a weekly basis, with a rough yearly overview to set the equipment maintenance timeline. This is mostly done by using methodologies and tools created almost half a century ago, using historic experiences and a limited dataset to steer the planning process.
And in a predominant number of cases this process willfully ignores at least one, if not more of the key factors – most often the changing prices in the electricity market are not a part of the planning equation. But if you include all the relevant factors into your planning, and look at production planning from a slightly different perspective, you could come up to very different conclusions.
Is summer really the best time to do maintenance?
For example, the logical time for any major maintenance work on gates, turbines and generators is summer, when water levels are usually lower. But, as we’ve witnessed throughout the last decade, due to increasing heatwaves during summer months the demand for electricity can surge during this exact period. If you as a planning manager rely only on previous experience and established routines, rather than being informed by an intelligent system driven by weather data and pricing changes, you could be missing out on a lot of revenue.
Also, forecasting the water flow and upcoming water value only based on local weather forecast and expected rainfall in the next 24 to 48 hours is useful, but not precise enough. This simplified method doesn’t take into account the surrounding factors, such as the dryness of the soil surrounding the river, the air temperature and associated evaporation of precipitation, and many other factors which will influence water levels in the upcoming days.
On top of that, in recent years we have witnessed a lot of Black Swan events in various geographies, happening after what seemed to be “just another rainstorm” and not even falling that close to the plant. As the climate change is taking its toll on the global water cycles and wind patterns, even a regular afternoon shower can quickly turn a quiet stream into a raging river, affecting the environment of your plant, but also your equipment, and disturbing your production plans in the most sensitive moment – when end users really need the electricity you’re producing.
Case Study
Optimization opportunities are everywhere
Price volatility has become a real concern throughout Europe over the past five to seven years. With the wholesale electricity price in the UK projected to drop below 50 GBP/MWh by 2030, any optimization that brings by a 1/3 more revenue is something that any operator should consider implementing.
An illustrative example comes from a mid-sized hydropower plant in Europe. The plant has two reservoirs, an upper one driving four turbines with a total installed capacity of 140 MW, and a lower one controlled by a single gate. Regulatory constraints prevent the operator from significantly reducing the water level in reservoirs, so the window of optimization opportunity based on water value is relatively small, around 7%.
To manage this plant the operator is using a modern hydropower plant management system developed by HYDROGRID, which allows them to run the plant in a very efficient and pro-active manner. This system takes into account the upper and lower water level limits of the upper reservoir, the downstream flow limited by local authorities, and the price oscillations on the electricity market, and delivers a production plan suggestion.
Thanks to the price-driven production plan delivered by HYDROGRID Insight, this plant’s operator is able to remain within all the water limits and focus on producing only at times when the price was above the certain threshold. In September 2024 they have set this threshold at 70 GBP/MWh, and this has brought the operator an increase of 34% in revenue over the production which would be based on non-optimized plans.
The plot below follows production planning, production actuals, energy prices and price forecasts, reservoir level and level forecasts and hydrological inflow and inflow forecasts.
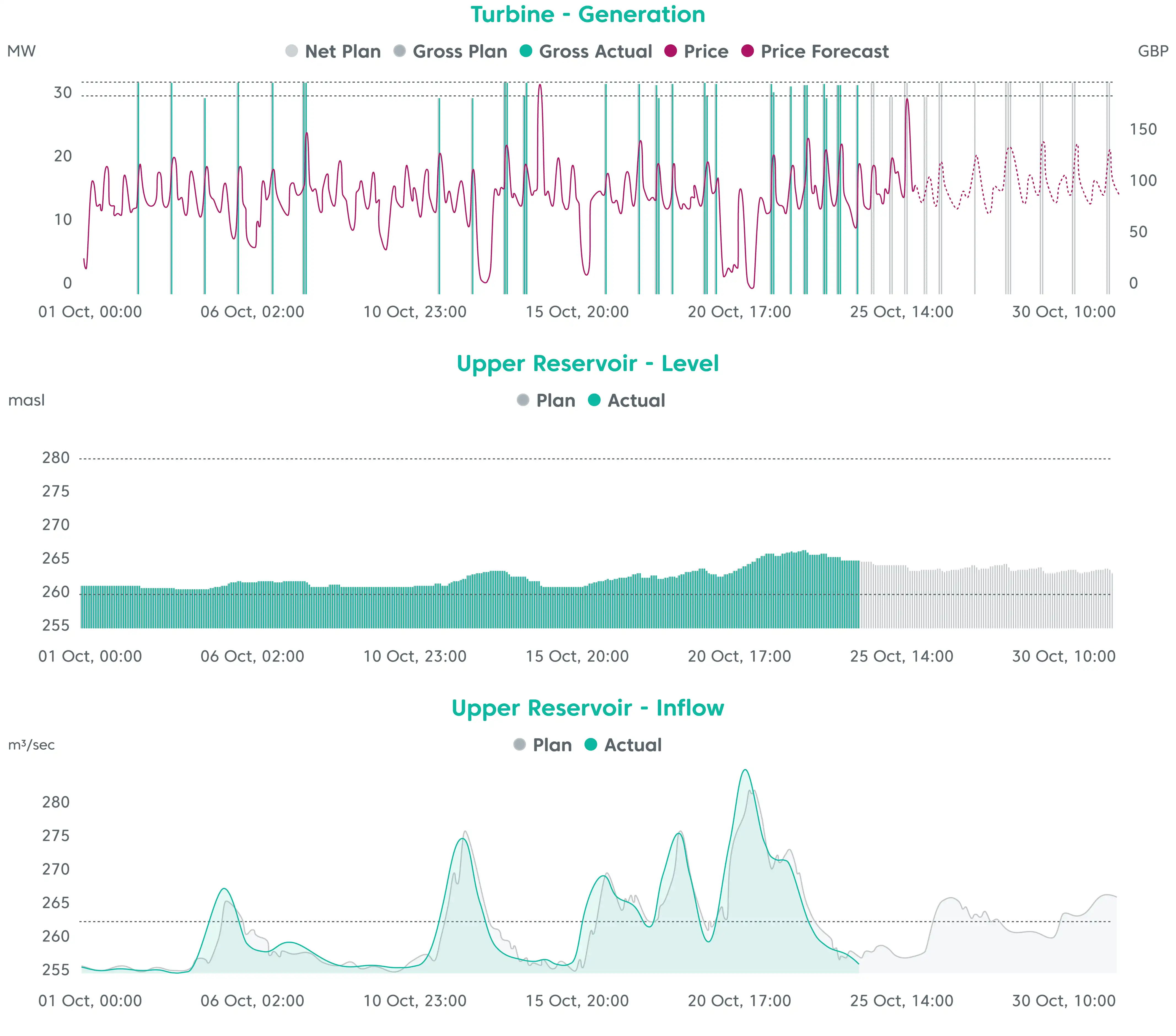
All actual values are shown in teal green and all planned or forecast values are shown in gray. When the price falls below the water value, as predetermined for this plant, water is being stored for future dispatch, and day-ahead production planning follows tis principle. The dotted horrizontal lines represent reservoir bounds, environmental and production restrictions associated with this plant
The reservoir level flexibility is marked with the two dotted lines on the Reservoir Water Level chart. You can follow how a stop in production translates to imperceptible increases in water level, as this flexible plant has a sizeable reservoir. Nevertheless, the upper or lower bounds are always prioritised by price driven dispatch algorithms.
Hydropower has a few aces up its sleeve
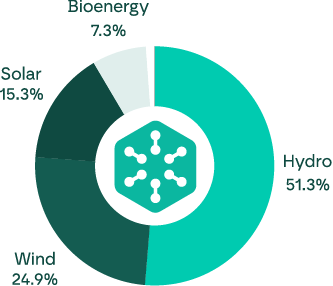
The massive shift towards renewable energy sources, such as wind, solar or biomass, is helping nations and organizations to significantly reduce carbon emissions and overall pollution. This is exactly why installed renewable capacities have been growing at an unprecedented rate during the past two decades. With hydropower becoming a key element of this energy transition, operational efficiency has been one of the rising topics in the community.
Although deemed successful so far, the energy transition has brought rising demands for electricity in developed countries, significantly affecting grid stability in many areas. In the past 20 years, hydropower has shown to be the key element in stabilizing the grid and enabling secure delivery of “green” electricity to consumers of all types.
This has allowed hydropower to take the cornerstone position in electric power production in many countries, but has also brought increased pressure to deliver more. And since it’s highly unlikely that the increased production will come from newly installed capacities, it is up to the operators to try to get the most out of the existing resources.
As other renewable energy sources cannot offer an equal level of agility, offering ancillary services has shown to be a key argument in favor of further investments in hydropower, contributing to the overall stability of the grid and intra-day flexibility.
Adopting Different Approaches for Different Plant Configurations
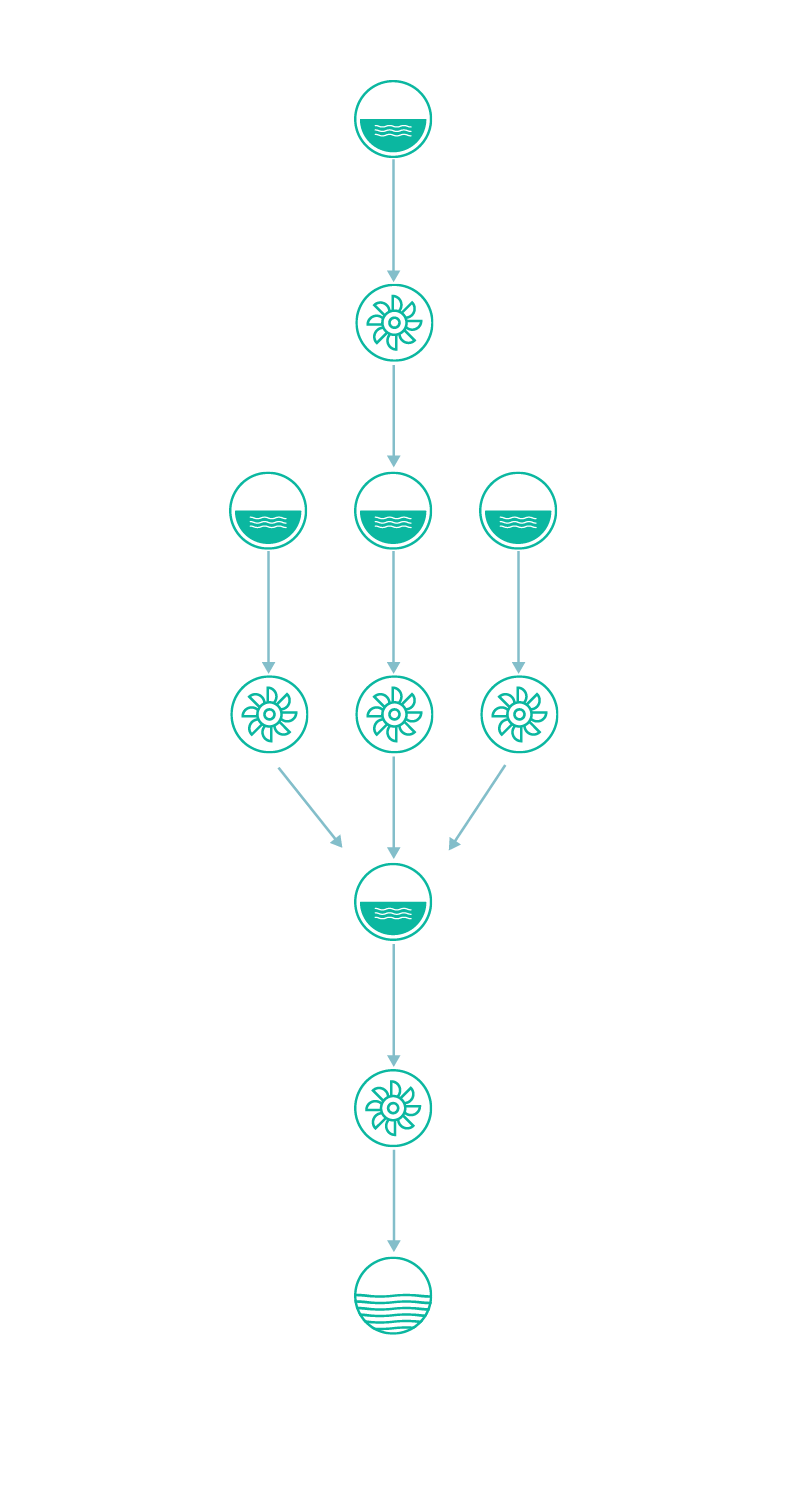
Optimizing production based on previous experience with available water levels and water value is often used as a strategy which brings less uncertainty in daily operations and secures environmental compliance, but also brings loss of potential revenue as a consequence. This is why many operators are looking for a sophisticated management control system, which could help them in squeezing additional value out of the available plant resources and delivering better business results without major changes to daily operations.
This is particularly relevant for small hydropower plants operators, who may currently not be pressed to optimize production plans, but as the competition grows and the demand for renewable power increases, the operational methodologies that worked well in the past 10 or 20 years might not be enough to keep your plant in sustainable business for the next decades.
With highly volatile wholesale electricity prices, successful planning became increasingly difficult for small and medium-sized hydropower plant operators. Some markets have even seen requests for 15-minute planning increments, and with this level of granularity intraday planning with usual tools becomes extremely difficult, if not impossible. Also, as the complexity of the plant’s configuration grows, proper calculation and forecasting definitely go beyond the limits of standard spreadsheet tools. And nobody likes to see those negative prices in monthly balance sheets.
There’s a limit to what you can achieve with Excel
Even if you manage to somehow cram meteorological data and current water reserves into a single Excel sheet, incorporating complex, interconnected factors such as multiple cascades or an ever-changing wholesale price into the calculation is out of the question.
Let’s take an example of hydropower plants with multiple cascades, where optimal operation is a nonlinear optimization problem with many variables and constraints. In a scientific paper “Optimal operation of cascade hydropower station based on interior point method” published at the 2021 International Conference on Power Engineering, a team of researchers from China have used the interior point method to solve the optimal operation of a 4-stage cascade hydropower station with intermountain runoff flows going into the reservoir. The optimization which used an algorithmic approach, just like the one used in HYDROGRID Insight, brought an increase of 6.7% in power generation, in comparison with a manual method of calculating expected power production in a complex environment with limited water resources.
So, it is clear that modern methods of calculating water value and potential electricity outputs present a much better basis for creating production plans, particularly for day-ahead and intraday planning. If you have at your disposal an automated control system that continuously monitors all vital parameters of your plant, the surrounding environmental factor, and the current state of the market, you can create both short-term and long-term plans much easier and faster, with greater confidence and reduced risk.
Mastering Equipment Maintenance and Renewal Planning
More agile and forward-looking hydropower plant operators have been considering introducing more modern solutions for operational management, but the most common obstacle they face is the lack of automation and management features in the equipment they are using.
Unless a plant was built in the last two decades, most of the equipment used in it has a low level of digitization, and connecting it to modern control systems is either very difficult or impossible. And operators don’t have the luxury to wait for another decade or two before they can replace the gates, turbines, generators and other key equipment with more modern, digital-native solutions.
Fortunately, there are interim solutions that can be used to digitally transform existing hydropower plant equipment. Installing sensors on critical plant components allows for continuous monitoring of operational parameters like water flow, generated power, operational and transmission losses, but also additional factors like vibration, temperature or pressure, vital parameters for successful predictive maintenance.
These sensors collect data which can be analyzed to detect anomalies indicative of wear and tear, or impending equipment failure. Vibration sensors detect changes in the oscillation of mechanical components, temperature sensors monitor excessive heat levels in equipment, while pressure sensors in hydraulic systems ensure that pressure levels remain within safe limits.
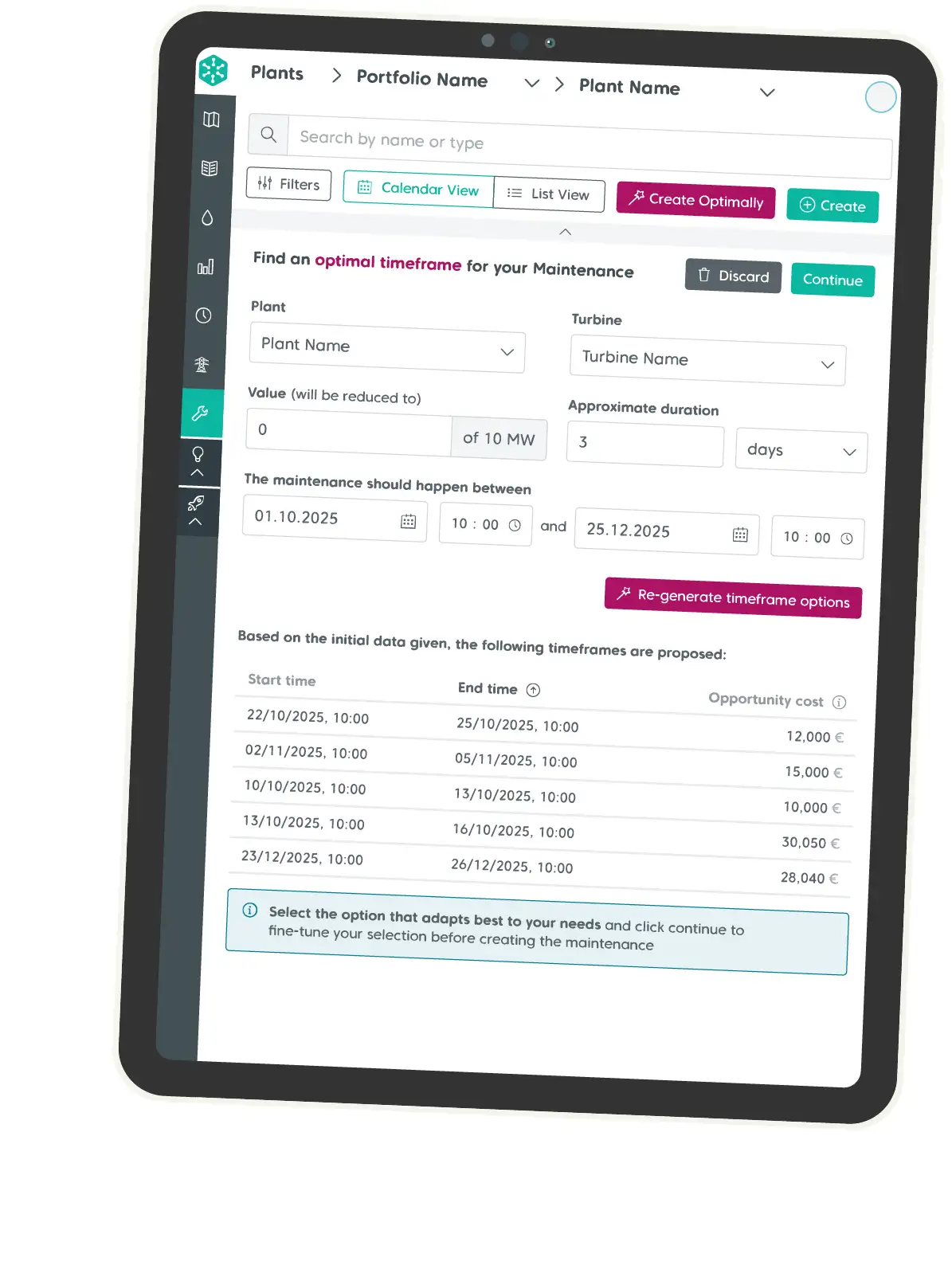
Optimal maintenance timing based on data insights
Even without sophisticated sensor networks, plant operators can benefit from strategic maintenance planning. Other relevant data that can inform maintenance planning is historical inflows, production and power prices. Here is an example of data informed maintenance planning.
Many operators, however, decided to add even more intelligence into the maintenance planning process. A combination of operational and maintenance benefits drove the Tennessee Valley Authority (TVA), a federally owned electric utility corporation in the United States, to implement optimal maintenance across its fleet of 30 hydropower stations. TVA’s approach involved deploying a network of sensors and developing machine learning models tailored to their specific needs.
This highly sophisticated solution continuously analyzes data and can provide real-time alerts to maintenance teams. As a result, TVA has seen a notable decrease in unplanned outages, extended the operational life of its assets, and achieved an annual reduction of 9% in operating and maintenance expenses, saving tens of millions of dollars in the process.
Even without sophisticated sensor networks, plant operators can benefit from strategic maintenance planning. Other relevant data that can inform maintenance planning is historical inflows, production and power prices. Here is an example of data informed maintenance planning.
Overcoming Equipment Aging with the Help of a Digital Twin
The Itaipu Dam, one of the largest hydropower plants in the world, with an installed capacity of 14000 MW, has been undergoing a major equipment renewal project for over two decades now. By using a combination of SCADA systems and digital twin technology, the operator of the plant has been able to understand the effects of renewing or replacing any of the installed devices.
With some of the equipment at Itaipu being over 40 years old, and with no means of bringing it to the digital age easily, as some of its device manufacturers no longer exist, using a digital twin is not only elegant and safe, but probably the only way to estimate the effects of any type of major change in the configuration of such a complex system.
Using digital twins to test and simulate
Another successful method in using digital technology to simplify and improve daily operations and planning in hydropower plants is the use of digital twins, a virtual replica of a physical asset, such as a hydropower plant, which is updated in real-time with data from sensors and other sources.
This technology allows plant operators to simulate different scenarios and assess the impact of production plan changes or incidents on plant performance, without placing actual assets in any type of danger. With the use of digital twins, it is much easier to predict equipment failures and maintenance needs, through analyzing historical and real-time sensor data and identifying outliers and other anomalies.
This way operators can avoid unplanned maintenance events resulting in costly outages, and schedule maintenance activities at the right time and with minimal downtime. And this is applicable on any size of hydropower plant, from tiny run-on-river plants in remote mountain areas to huge plants with complex configurations and diverse equipment.
Breaking Down Organizational Silos
In smaller power plants everything seems to be much simpler, particularly when it comes to planning and operations. One to two people oversee the whole process, and communication is simple and efficient. Still, the issue of complex inputs and variables remains, and even the most skilled managers can have a hard time getting more out of the existing plans and resources.
In larger organizations, as the complexity of plant configuration increases or there are more plants involved, teams tend to start working in a more separate, siloed way. Everybody is focused on their jobs and responsibilities, often failing to see the wider picture and opportunities.
This is not something typical for hydropower plants; the same thing happens in practically any type of organization. And the way to resolve it is the same – managers need to break the barriers and find a way for teams to work in synergy, rather than having departments that don’t communicate efficiently with each other.
With the power of data, even the small players can win
The benefits of having a 360-degree view on all parameters relevant for production planning are clear even on the smallest examples. An operator of a small hydropower plant in Norway, with multiple cascades, a small reservoir and a single turbine with 2 MW capacity, uses HYDROGRID Insight to create production plans and implement them directly.
Even with such a small installed capacity and limited by a small reservoir, this operator has managed to increase their revenue in August 2024 by 39%. And they achieved this by optimizing production based on the recommendations provided by HYDROGRID Insight, based on the available water value, forecasted day-ahead prices, and water level and flow constraints set by local administration.
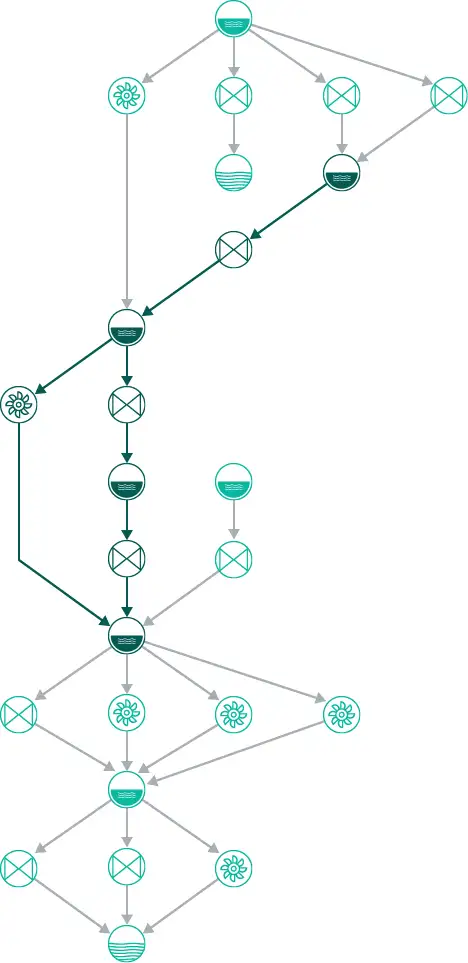
When people work together, miracles can happen
In hydropower this issue is magnified with the fact that production planning depends on inputs coming from disparate sources. You need to know the current state of the water value, the forecasted water inflow for the upcoming period, and real-time price changes on the electricity market. So, to create an optimal production plan, operations, maintenance and trading departments need to cooperate in an effective and seamless way.
Normally the O&M teams work on their own, with whatever planning tools are at their disposal, and occasionally sync with trading to make minor adjustments. Even in scenarios with simple hydropower plant configurations, day-ahead planning that doesn’t include key factors into a single decision support system can be way off and result in missed revenue for the operator.
Having that in mind, imagine what happens in more complex scenarios with multiple cascades or a pumped storage, and you’ll realize how important is to sync all the available data into a single source of truth. This would also save plant managers from organizing numerous sync meetings, because all the relevant data would be available to all team members, keeping them up-to-date and allowing them to make the right decisions.
On top of that, a lack of a centralized and updated data view hinders agile reactions to market conditions and proper intra-day planning. Imagine meeting every six hours each day to consult on production plans, and you’ll easily understand that this is definitely not the right way to do hydropower business. The year is 2024, people should really start using modern technology to their advantage, not just as a glorified calculator.
And let’s not forget the very important aspect of reporting to stakeholders. Having a fully automated control system in your hydropower plant can significantly reduce the overhead you are currently seeing when creating reports to various interested parties. This includes plant owners and investors, governmental bodies, but also the general public interested in operating practices of their electricity producers. And with a detailed history of your operations in a single place you’ll be able to answer any questions that might come from any of these stakeholders.
Integrating Environmental and Regulatory Constraints
Even if you got the planning, production, maintenance and trading parts just right, one large operational challenge remains – all hydropower plant operators face various regulatory constraints, mostly focused on environmental protection.
As a renewable energy source, hydropower is considered as “green” and safe for the environment, but there are also too many things that can go wrong if environmental factors are not considered. Clean water is an invaluable resource for humanity, and operators are tasked to protect it and the life and livelihoods it harbors.
Increased regulation presents one of the major changes in the hydropower industry in the past two to three decades. Operational practices that were previously allowed aren’t any more, and there are more and more new requirements from plant operators. Also, these new rules place many constraints on the core business of the plant – successfully generating and selling electricity.
Hydro digitalization: help or hindrance?
In an effort to compensate for environmental limitations, the Glen Canyon Dam on the Colorado river in the United States has integrated solar power and energy storage solutions into its hydropower operations. This integration has improved the flexibility of the power plant’s operations, mitigating the long-term drought effects, and has allowed the operator to quickly respond to oscillations in energy demand.
But to manage this hybrid system efficiently, they needed a powerful control system which is able to coordinate the operation of the solar panels, storage and hydropower turbines, ensuring optimal energy production. At the same time the system needs to provide enough water flow to maintain the connected ecosystems, and to prevent potential danger to a major touristic destination – The Grand Canyon, which lies downstream from the dam.
Given the size of the whole system at Glen Canyon and the Lake Powell reservoir storage, any attempt to cover surge demand for electric power with a sudden change in water release could trigger major environmental damage, including higher greenhouse gas emissions. A set of restrictions has been imposed on the operator in 1995, limiting the dam release in the range between 8000 and 25000 cubic feet per second (230 to 710 m3/s). This largely limits the operator to meet the growing demands for electricity production, causing an estimated annual revenue loss of over 50 million US dollars.
In such a situation, having a state-of-the-art control system, which considers both the potential and the limitations, helps the operator to recuperate some of the financial losses, while maintaining full compliance with regulatory requirements. Given the magnitude of the losses, even a single-digit percentage change could bring tens of thousands of dollars in recuperated revenue, making an investment in such a sophisticated control system very much worth it, even in the short term.
Embracing the Power of Digital
As the pressure on increasing efficiency rises, plant operators and managers are seeking new ways to utilize existing technologies and plant management solutions. If you are using telemetry data coming from gates, turbines and generators only to make decisions based on small datasets, you are wasting the potential of the data goldmine you’re literally sitting on. But this is yet another area where your advanced Excel files filled with VBA scripts, developed a decade ago, simply won’t cut it.
Modern management solutions use machine learning to analyze past data and to forecast future events based on the correlation of historical data points coming from weather services, your machines, and the trading desks. This way the control system can provide much more precise estimations of key factors, such as water levels, allowing the plant operator to optimize the production and maintenance plans accordingly.
Even small steps in modernizing a hydropower plant with digital tools can bring huge benefits, as the starting point is often at a very low level. Revenue gains ranging between 20 and 40%, with a disproportionally smaller investment in the digital solution, present a very interesting proposal for any business owner or planning manager.
Even if we look at this not only from a strictly financial perspective, an increase in plant productivity of 2-3% can bring a very much needed edge in an increasingly competitive market. Sounds logical and simple, but it’s clear that it’s actually very complex. And without the help of technology, you’d be pretty much lost in all of that complexity.
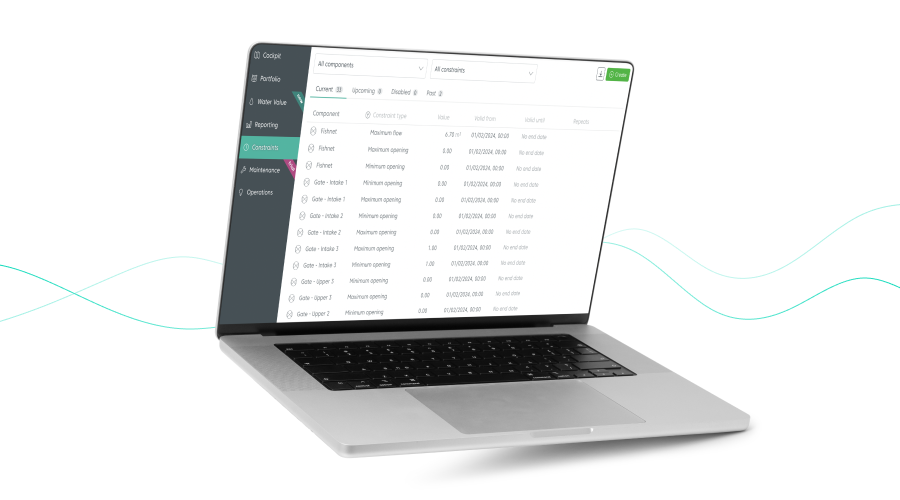
Conclusion
If you’re still using manual data inputs coming from different sides (water, maintenance, trading) to discuss production planning on weekly meetings gathered around Excel sheets, you are way behind competitors using more sophisticated plant management systems to create and implement optimized production plans.
Because all they have to do is look at the proposed plan variants and make a decision which production plan to use. And in some cases, the selected plan can be directly implemented, because a good management system can also “talk to the machines” – the gates, turbines and generators.
You can look at modern plant management solutions like HYDROGRID Insight as a decision support system, which reduces risks and improves operations and profitability of your power plant. Through bringing production planning, maintenance and trading departments together in a single, centralized view, this solution also breaks the organizational silos.
HYDROGRID Insight control system can work with existing remote sensing data coming from your devices, create a production plan, and feed it back to plant or let you decide. This digital management solution can also work just with manually entered data (such as your water levels), and provide a plan which a production manager can accept and implement, or decline and then tryout a different scenario based on other inputs or changed constraints.
Yes, it’s that simple, and just compare this with your daily struggle with multiple data sources and stakeholders. Sadly, this doesn’t mean that you can offload your job as a production planner to the machine and go home to watch football, but the whole process could be much more elegant and seamless, less prone to error, and delivering much better results. Isn’t this worth a try?
Schedule a demo of the HYDROGRID Insight today and see for yourself how you can increase efficiency of your hydropower plant with the benefit of using modern technology.
Get in touch with our hydro consultants to learn how!